絶対に
あきらめない
気持ちが、
大空への道を
開いた。
2006年、5軸制御マシニングセンターを導入したばかりの大日製作所では、この最先端設備のポテンシャルを活かして新たな事業領域に参入したいと考えていた。
そして、「航空機業界参入支援プロジェクトのためのセミナー」に当社の代表を務める橋本が参加したことをきっかけに、
社内にプロジェクトチームが立ち上がり、
大日製作所の空への挑戦が始まった。
今回は、当社の航空機業界への参入の道を切り拓いた3名の技術者に集まってもらい、当時の様子やそれぞれの想い、その経験から見た会社の魅力などを語り合ってもらった。
話を聞いた3名
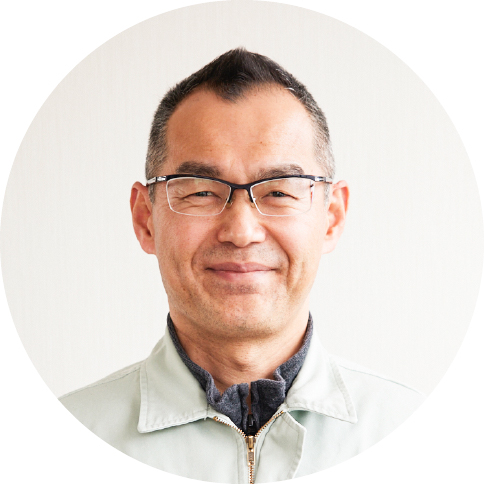
製造部
生産技術課
K・I
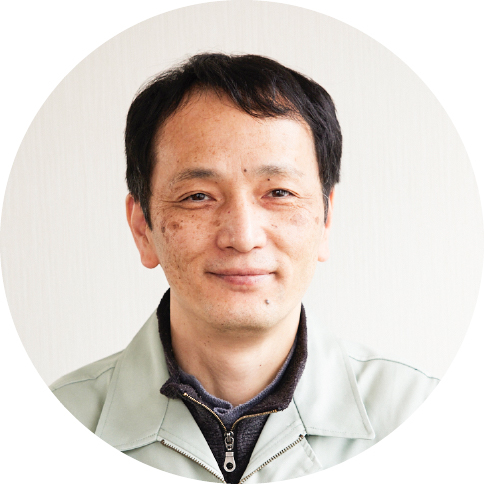
製造部
機械加工課
T・T
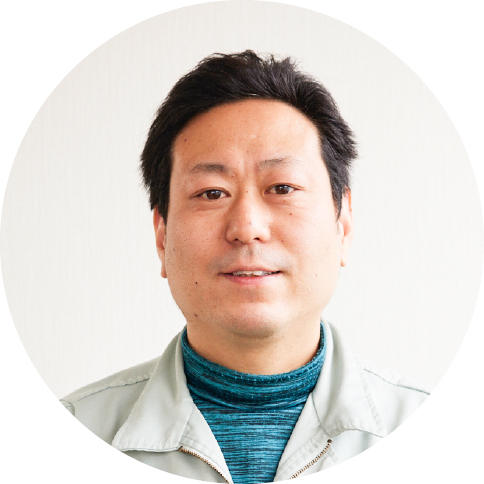
品質
保証部
S・M
プロジェクトが始まるまで
橋本はセミナーに参加後、航空機業界のある大手部品メーカーに対し、「大日製作所も航空機業界へ参入したい」という意思を伝えた。しかし、返事は「No」。航空機業界は実績を重んじる風土があり、まだ何一つ実績のない大日製作所は相手にされなかったのだ。それでも橋本は必死に担当者にアピールを続けた。すると、あるとき、「これができたら取引を考える」と言って、ある製品の一枚の図面とサンプルを渡された。橋本はその図面を詳しく確認することなく、迷わず「できます」と返答。急ぎ会社に戻り、プロジェクトチームを立ち上げた。
そこに完成品が
あるのなら、
つくれない
はずがない。01
—当時、皆さんはどういうきっかけでプロジェクトに参加していったのですか?
当時、僕は船舶関係の部署で働いていて、5軸加工もやり始めたばかりでした。
そこに社長が一枚の図面を持って登場して、「できるか?」と。そう言われると、私は勝手に「できない」ではなくて「どうやるか?」を考えていました。
僕は入社前の面接で、急にその製品のサンプルを見せられたんですよ。「これ、つくれますか?」って。
目の前に実物があるということは、どこか他の会社ではつくることができたんですよね。だから、素直に「やれます」と答えました。
僕も入社してすぐのタイミングだったと思います。航空機業界への参入を検討しているという話は少し前から聞いていました。
もともと、品質検査の部署に所属していたのですが、あるとき、3DモデリングソフトのCADが使えるかと聞かれて、「使えます」と答えた結果、日々の業務と平行しながらこのプロジェクトに参加することになったのです。
—皆さん、「できるか?」とか「使えるか?」とか聞かれて、「はい」と即答するのがすごいですね(笑)。
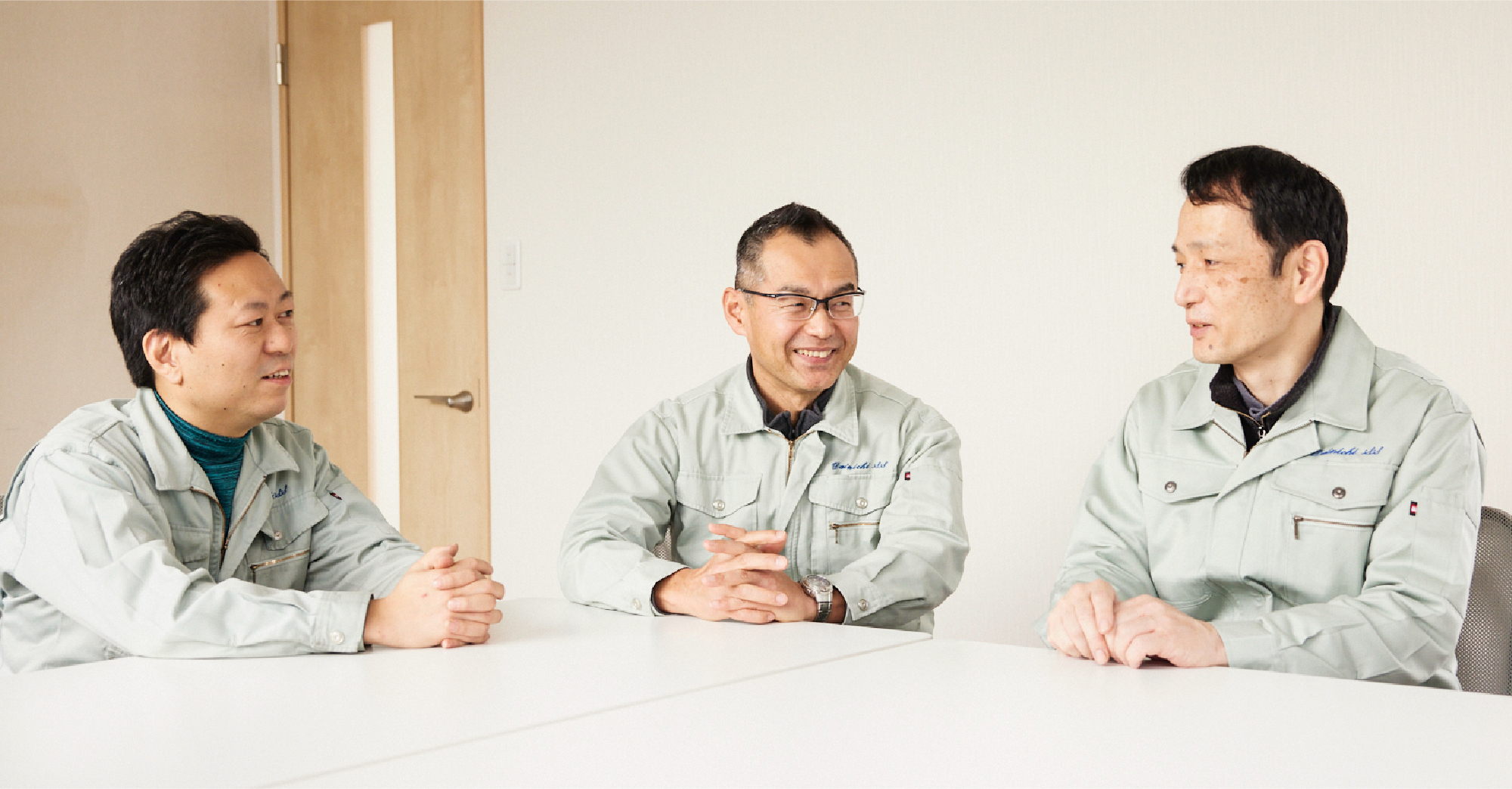
ちょうどその頃、会社として新規事業を開拓していこうということが決まり、新しいことにはみんな次々と挑戦するような雰囲気だったんですよね。
社⻑がずっと新しいものを追いかけていることも、みんなよく理解していました。
加⼯⽅法も、
測定⽅法も
すべてが未知の世界
—では、そこから早速、その部品の製作に取り掛かったのですね?
はい。しかし、⾯接では「できる」と即答しましたが、実際はまったく⻭が⽴ちませんでした(笑)。
取り掛かってから何ヶ⽉経ってもうまくいかなくて、悔しかったなあ。チャンスをくださった担当者にも毎回、「まだ、できていない」という報告しかできなくて…。
でも、社⻑は「できるまで頑張ろう」という姿勢を崩さなかったですね。
品質検査の担当としては、検査の準備をしつつ、製品が上がってくるのをずっと待つことしかできませんでした。
航空機部品となると、それまで⾃分たちが携わってきた製品より、とても厳しい検査基準が設けられているんです。
さらに、検査記録をきちんと書類として提出する義務もありました。初めてのことばかりで、不安も⼤きかったですね。
当時、検査するための測定器そのものも新しくしましたよね?
そう。測定器⾃体もより精度の⾼い検査ができるものを準備していました。ただ正直、うまく検査できるか⾃信がない部分もありましたよ。
本当に、加⼯にしても、測定にしても、何もかもが初めてのことばかりなんです。図⾯だって、あんなに複雑かつ緻密なものは初めて⾒ました。
「幾何公差」という検査基準に関する指⽰も、図⾯にびっしりと書かれていて。「あ、これは難しいな」と⼀⽬でわかりました。
そうそう。図⾯を読み解くのすら、難しかった。後から知ったんですが、当時、あの図⾯で正確に製品をつくる企業は⽇本で⼀社しかなかったそうです。
だから、⼤⼿部品メーカーの担当者も、その⼀社以外につくる会社はないかとずっと探していたみたいです。
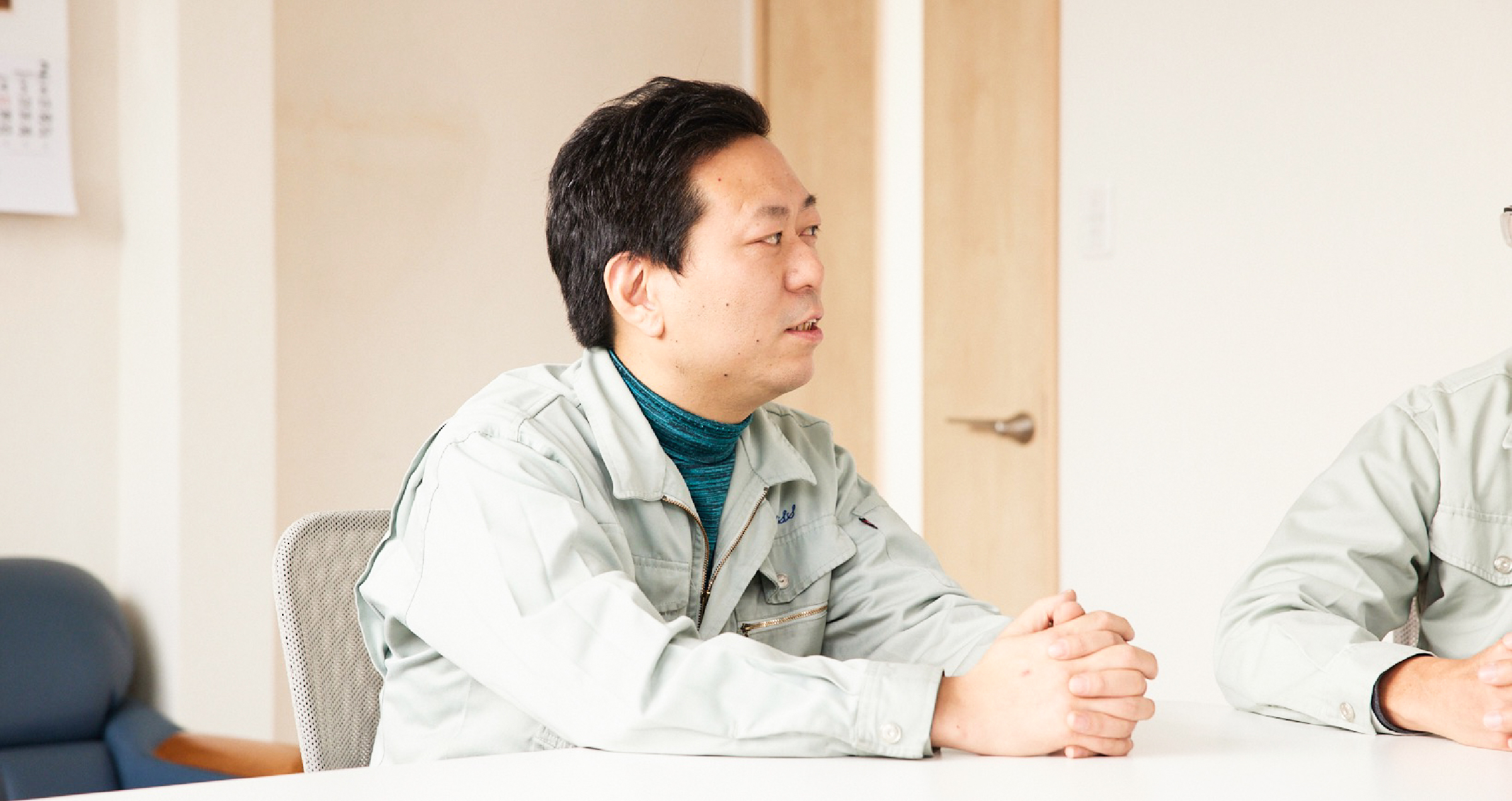
僕らの
挑戦する意識が、
会社の風土を変えた02
—想像以上に苦労の多い開発だったんですね?
最初から壁の連続でした。CADで図⾯を3Dに起こして、ソフト上のシミュレーションをかけるとうまくいくのに、
実際には思ってもいない部分にぶつかって加⼯できなかったりするんです。⼿で製品を触りながら、感覚で加⼯するようなこともありました。
当時は、今のようにロボットのアームがプログラム通りに動いて加⼯してくれるというわけではないですからね。
全部⼿動で加⼯しては失敗して、をくり返すわけです。
途中から、⾃動加⼯になったから良かったけれど…。
僕の場合は、⼊社してすぐにこの仕事だったので、機械の操作も全部⼀から覚えながら必死に取り組みました。
材料費も⾼いから、失敗もできないし。
仕事が終わっても、頭の中は「どう加⼯しようか」ということでいっぱいでしたね。
ようやく形になっても、検査で測定をしたときにサイズに誤差ができてしまったのは悔しかった。
何度もS・Mさんから戻ってきて、そのたびに⼀からやり⽅を変えてみるんです。
というのも、航空機部品ということもあり、この製品は通常よりも軽さと薄さを求められたんです。
そのぶん、加⼯の際の固定⽅法によっては、製品そのものが変形したり、ズレが⽣じたり。
製品となる材料のつかみ⽅ひとつからやり⽅を⼯夫しなければならない、とてもデリケートな仕事でしたね。
検査から戻されるたび、⼯具もつくり直し、治具もつくり直し。
あのときは「社⻑、もうあきらめてくれないかなあ」なんて気持ちすら芽⽣えました(笑)。
まあ、そのぶん、最終的に社内での検査をクリアしたときはうれしかったけどね。
でも、ひと安⼼も束の間ですよ。次は依頼してくださった部品メーカーでの測定が待っていて、その段階でダメだったらまたやり直しという可能性もありましたから。
最後の検査でOKが出るまでは不安でしたね。
たしかに。たとえば、ネジは温度の変化によってわずかに縮む性質を持っていますから、完成時はOKでも時間が経ってダメになっていることもあるんです。
だから、材料の特性もしっかり考慮しなければならないし、社内で検査をする私も細⼼の注意を払うように⼼がけていました。
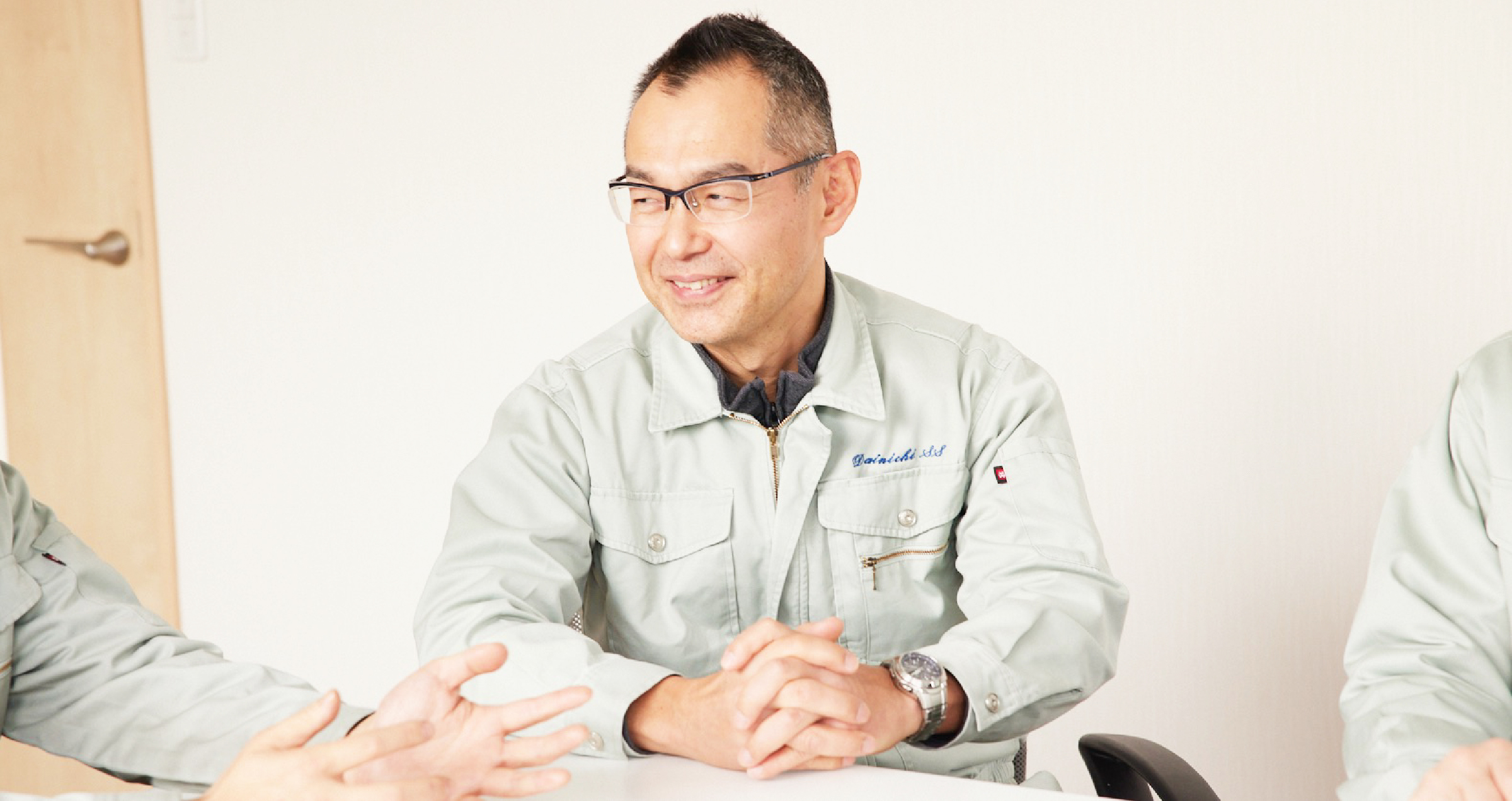
—なるほど。そうして、いくつもの壁を乗り越えて合格し、航空機業界への参⼊を果たしたんですね。
そうですね。振り返ってみると、⻑い戦いだったなあ。プレッシャーも⼤きかった。
気持ちはわかります。⼯場内でも加⼯機を⽌めて僕らが悩んでいると、「何をしているの?」という視線を感じましたしね。
そうですよね。この挑戦の以前は、当社でもこれほどまでに難しい仕事はしていなかったから、加⼯機が停⽌することもあまりなかったんです。
でも、私たちは機械を何度も⽌めては考えている。周りから⾒ると「そんなことをしていて、本当に売り上げにつながるの?」という感じだったと思いますよ。
⼀⽅で、「こうしてみたら?」という意⾒をくれる⼈もいたよね。
私たちが悪戦苦闘しているのをみんな⾒ていたから、ある意味、挑戦するという意識というか⾵⼟が広がっていくきっかけにもなったかなと思います。
たしかに。それまでも挑戦する姿勢はあったけれど、ここまでのレベルのものはなかったですからね。
⾔い⽅を変えれば、最初に私たちが⼀番難しい仕事に挑戦したことで、⼤⽇の挑戦のレベル⾃体もひとつ上げたのかもしれませんね。
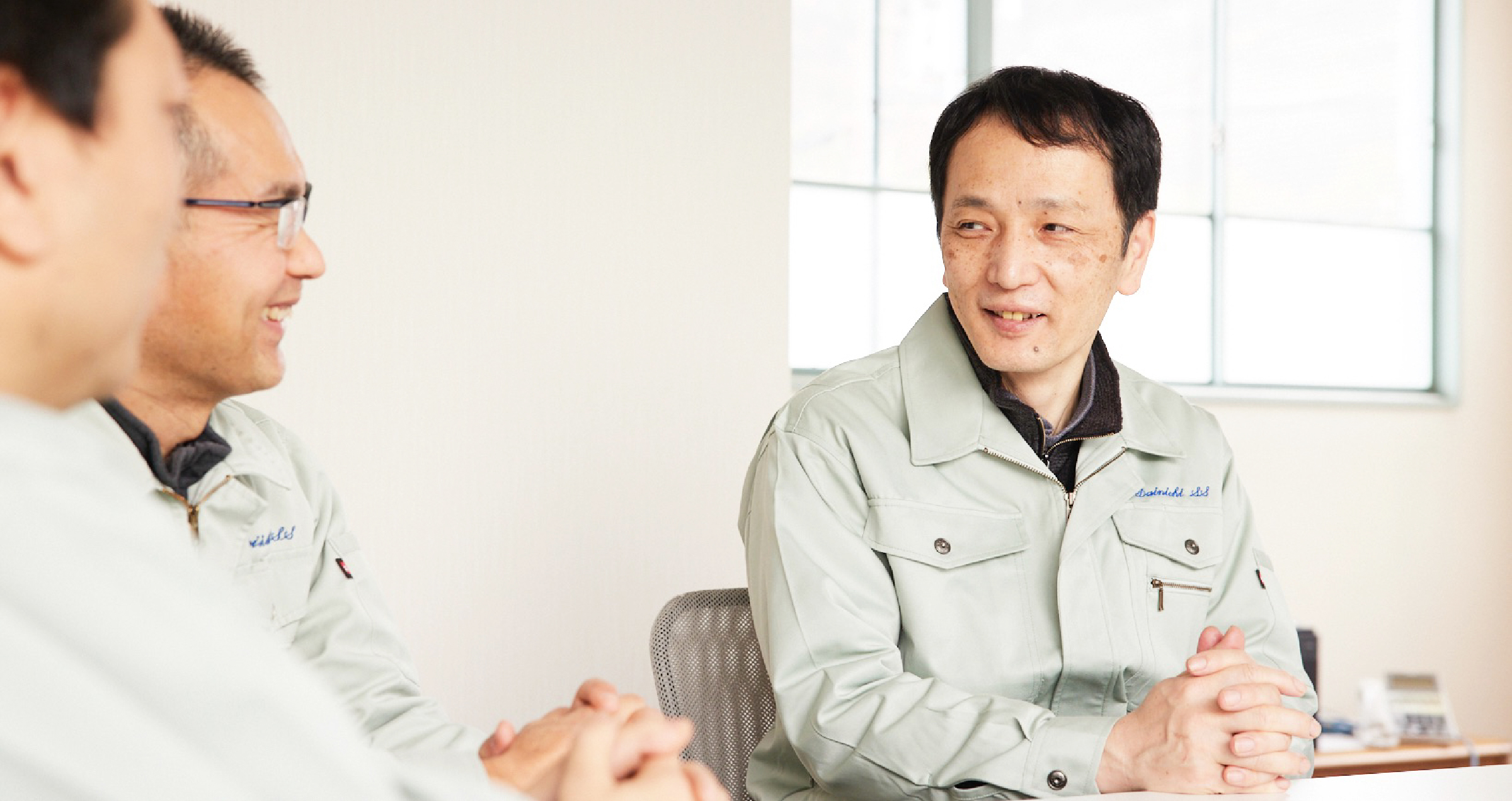
「⼤⽇さんだから」
と
依頼されることが
⼤きな誇り03
—今回のプロジェクトを通して、得られたものはなんですか?
私たちは⽇頃、⼯場で仕事をしているため、お客様から直接お礼を⾔われるような機会はなかなかないのですが、
その⼤⼿部品メーカーから感謝状をいただきました。
そう。その部品メーカーの膨⼤な取引先の中で、毎年⼀社にしか送らない感謝状とのことで、とてもうれしかったですよね。
私たちの挑戦を⽪切りに、ずっと、お付き合いを続けられていることに対する感謝の気持ちということでした。
ここ10年で受注する製品の種類もとても増えましたからね。こちらとしても、ありがたいですし、あのとき頑張って本当に良かったと思います。
最近では、他社では実現が難しいという理由で、当社に依頼される製品も増えましたよね。
「⼤⽇さんだから」とお願いされるのは誇らしい気持ちになりますし、そのぶん、期待に応えなくてはと⾝が引き締まる思いもあります。
僕の場合、本業は品質検査ですが、このプロジェクトでCADのスキルを⾝につけられたので、⾃分の仕事の幅がぐっと広がったと感じますね。
それまでよりも図⾯をつくり⼿の⽬線で⾒られるようになって、製造過程全体を意識しながら検査できるようになりました。
私は今回のプロジェクトを通じて、ひとつひとつの材料に対する知識、治具設計のスキル、複合加⼯機械の特性を活かして効率的に加⼯する⽅法など、
さまざまな知⾒を得られたように感じます。
できることは⼀気に増えたよね。
はい。それに加えて「やってみれば、なんとかなる!」というマインドを⼿に⼊れられたことも⼤きかったですね。
最初はどうなるかわからなかったけれど、試⾏錯誤しながらもここまでこられたことで⾃信につながっているのかなと。
それは私も同じです。ひとつのものをつくり上げるために、たくさんの経験をしてきました。当然、失敗もありますが、じつはその失敗が別の仕事で活きてきたりもする。最終的には、⾃分⾃⾝の引き出しがどんどん増えていくんですよ。
そして、それは会社の引き出しにもつながっているように感じます。当社ほどさまざまな業界の多様な製品をつくっている会社は少ないのではと思いますね。
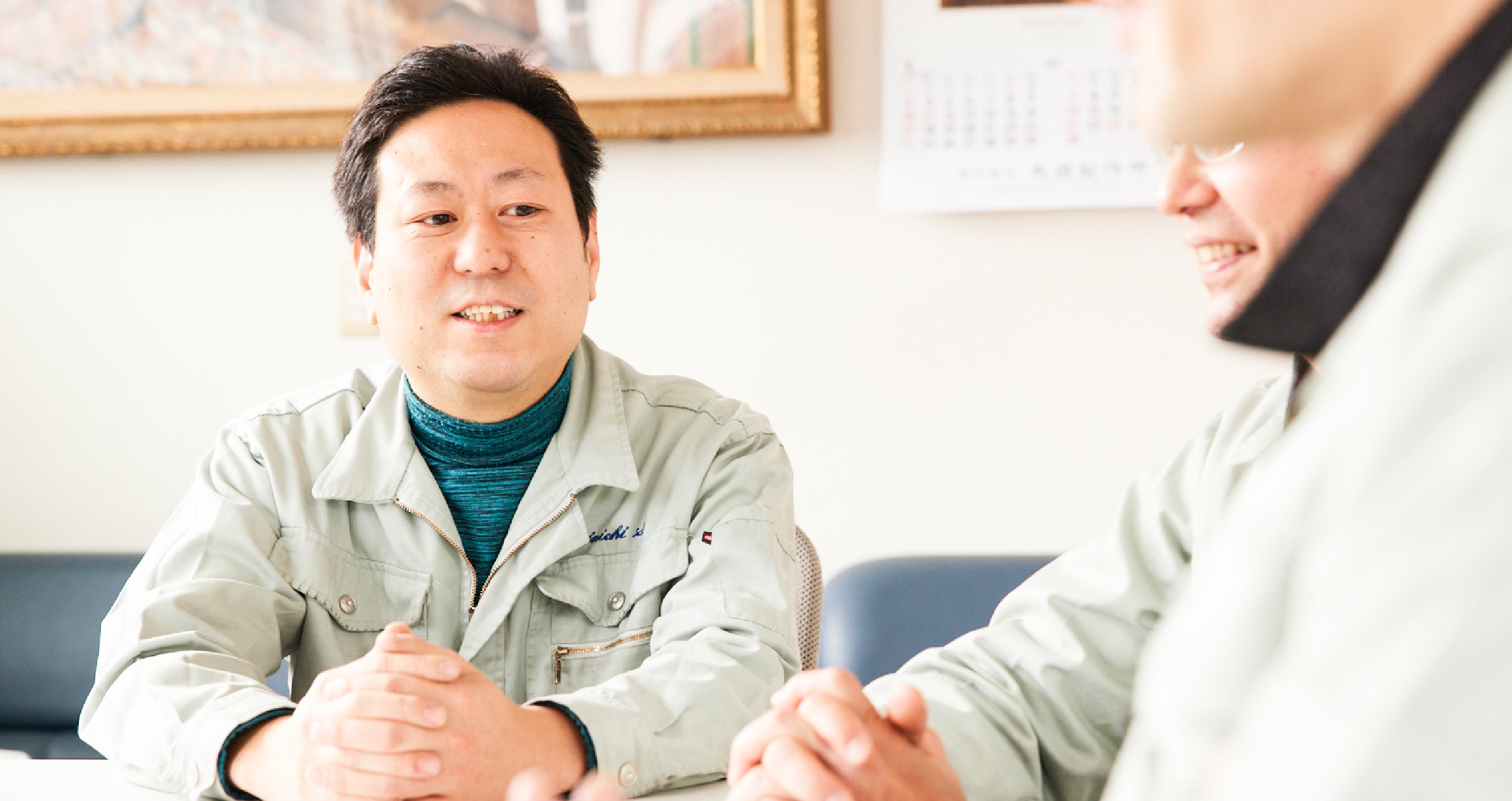
より使命感の強い
仕事を求めて、
上を⽬指し続ける04
—今後、皆さんはどのようなことに挑戦したいですか?
過去に⼀度、依頼されたのに完成までたどり着けなかった航空機部品がありますよね。僕は、まずはそのリベンジが⽬標です。
そうですね。航空機部品の中には、わずかな誤差でも乗客の命を危険にさらすかもしれない部品もあります。
だからこそ、私たちの技術レベルをそこまで引き上げて、より⾼い品質を世に送り出したいですね。
それから、航空機関連で⾔えば“宇宙”というキーワードは社⻑の⼝からよく聞きます。
だから、宇宙産業への参⼊の可能性はあるんだと信じています。再び苦労するのかなと⼼配な気持ちもあるけれど、これからが楽しみですよ。
⾃分たちがつくった部品が、宇宙に⾏くと思うとワクワクしますね。
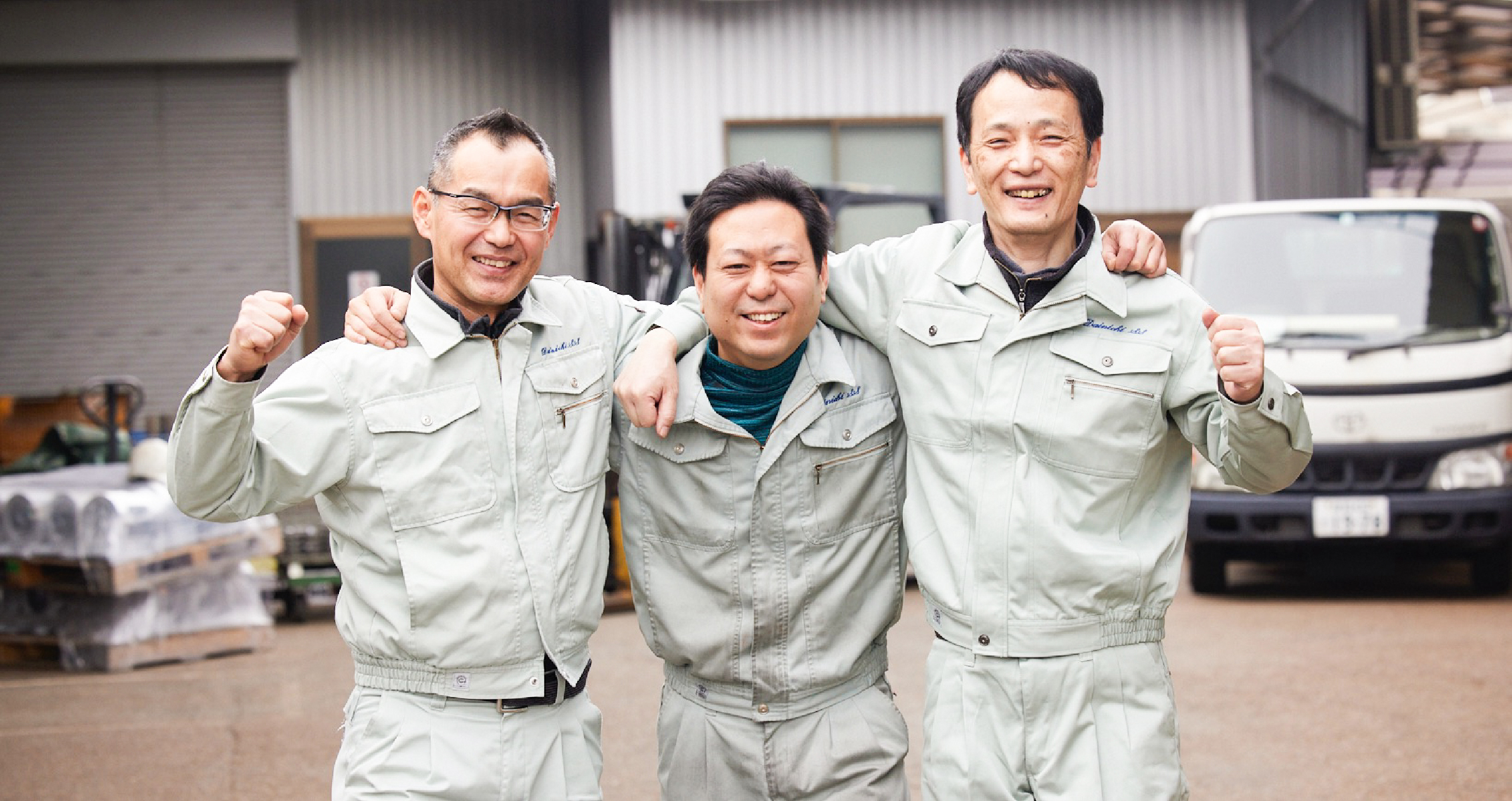